Our Process
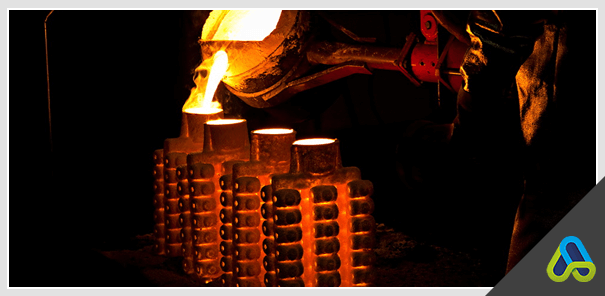
What is Investment Casting?
Investment casting, also known as lost-wax casting, is a meticulous manufacturing process that dates back thousands of years. This ancient technique has evolved with modern technology to create intricate, high-quality components for a wide range of industries.
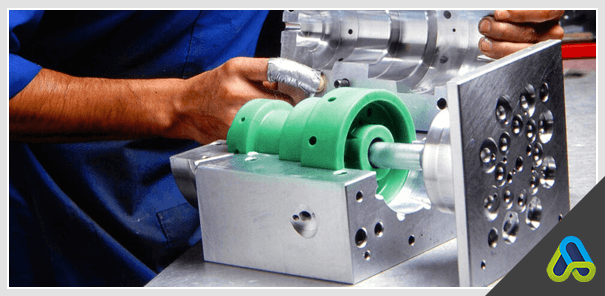
The Investment Casting Process
- Pattern Creation: Our process begins with the creation of a wax or plastic pattern. These patterns are made using state-of-the-art machinery or hand-crafted by skilled artisans, depending on your project’s requirements.
- Assembly: Multiple patterns are attached to a central wax tree to create a cluster. This tree is then coated with a ceramic shell to form a mold.
- Dewaxing: The ceramic shell is heated, causing the wax or plastic to melt and flow out, leaving behind a cavity in the mold that perfectly replicates the desired part.
- Preheating: The ceramic mold is preheated to ensure it can withstand the extreme temperatures during the casting process.
- Casting: Molten metal, typically poured at temperatures exceeding 2000°F (1093°C), is poured into the mold cavity.
- Cooling: The mold is allowed to cool and solidify, forming the final part. This cooling process can take hours or even days for larger and more complex components.
- Shell Removal: Once the metal has solidified, the ceramic shell is removed, revealing the finished part.
- Finishing and Inspection: The cast part is carefully inspected for quality and accuracy. Any necessary finishing touches, such as machining or polishing, are performed to meet precise specifications.
Advantages of Investment Casting
Investment casting allows for the creation of intricate and complex parts with fine details.
Tight tolerances and excellent surface finishes are achievable with this process.
A wide range of metals and alloys can be used, including steel, aluminum, titanium, and more.
Reduced material waste and minimal machining make investment casting a cost-effective choice.
It’s ideal for prototypes, low to high-volume production, and custom parts.
Investment castings cut down on labor time and produce quicker lead times because it greatly reduces the amount of machining required after casting.
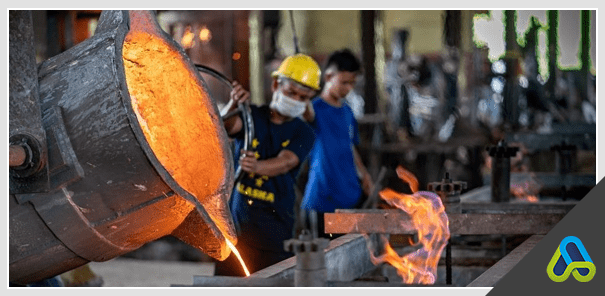
Applications of Investment Casting
Our investment casting process finds application in various industries:
- Aerospace: For lightweight, high-strength components.
- Automotive: Engine parts, transmission components, and more.
- Medical: Precision surgical instruments and implant components.
- Energy: Turbine blades, nozzles, and other critical parts.
- Jewelry: Crafting intricate and delicate jewelry pieces.